WashU materials scientists combine supercomputers, 3-D printers to create strong metallic alloys
Replacing time-consuming trial and error, computational methods will be used to find new alloys for structural, load-bearing applications
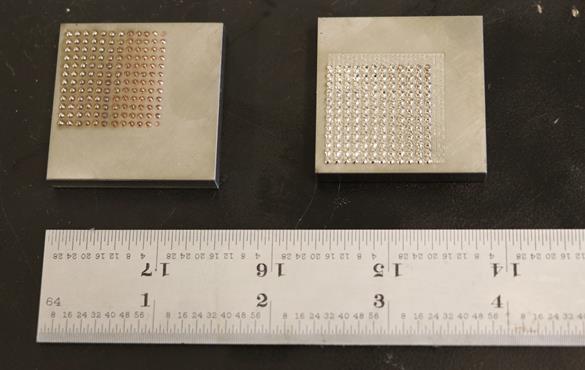
Research using quantum-mechanical computation will be used to identify combinations of elements that have the most promise for load-bearing applications
Engineers looking to create high-performance metallic alloys that are resistant to corrosion, fatigue and wear while remaining strong often use a trial-and-error method to find the right combination of elements. Now, engineers at Washington University in St. Louis plan to use computational methods and additive manufacturing to find the best combinations, saving significant time and money.
Katharine Flores, professor of mechanical engineering & materials science in the School of Engineering & Applied Science, will build on some foundational work in high-entropy alloys — single-phase substances of five or more metallic elements in relatively equal parts — to find new alloys for structural, load-bearing applications, such as in aircraft, power generators and energy storage devices. Instead of the time-consuming trial-and-error method, Flores will work with Rohan Mishra, assistant professor of mechanical engineering & materials science, who will use quantum-mechanical computation to identify combinations of elements that have the most promise. Once identified, Flores will synthesize the alloys using a laser-aided metal-on-metal deposition technique to create a library of potential alloys for further testing.
With a three-year, $496,077 grant from the National Science Foundation, Flores and Mishra will use these methods to look for high-entropy alloys that can withstand high temperatures. Mishra will perform the computational calculations on some of the most powerful supercomputers to identify promising candidates from a large composition space. Then Flores will use her lab's technique to create a 2-D library, a one-inch square piece of metal on which about 100 tiny dots of individual candidate alloys can be fabricated. Flores' laser-deposition technique creates the library in about 30 minutes with just a few grams of material.
The additive manufacturing technique is similar to polymer 3-D printing where the machine draws the material onto a surface layer by layer. However, Flores uses a laser to melt a small region of a base material, then adds up to four different powders to the melt.
"What we're doing with this research is changing the composition of the powders as we raster the laser across the surface, and there are a few ways we can do that," Flores said.
"We can change the composition of the powder continuously to produce a gradient, or we can make individual dots with different compositions."
While Flores has been doing similar work in bulk metallic glasses for several years, the high-entropy alloys are a new class of materials generating significant interest, she said. One particular attribute that is appealing is that the materials don't undergo phase separation, or become less homogenous at different temperatures as other metals do.
"On the calculation side, Rohan is going to identify combinations of elements that produce a single phase or produce an interesting combination of other phases," said Flores, who also is director of the university's Institute of Materials Science & Engineering. "He will tell us what combinations to try, then we will deposit those elements and do the microstructural characterization and mechanical property measurements to test the strength and stiffness and map out those properties."
Once Flores' lab has the measurements, she will provide them to Mishra, who can feed them back into his computational model to improve his predictions. In addition, Mishra's team will use one of the world's most powerful microscopes at Oak Ridge National Laboratory to look at the structure of the materials at the atomic scale.
In addition to accelerating the development of new alloys, the work will contribute to the growing field of additive manufacturing, which could be used to make complicated parts in a single manufacturing process.
"When making a part for an airplane that has 20 different pieces that need to go together, if you can make it in one piece, you eliminate all of the fasteners, which means less weight, improved fuel efficiency and reduced manufacturing and maintenance time," she said.
Previously, Flores' lab created 21 alloys with aluminum, cobalt, chromium, iron and nickel and tested them using X-ray diffraction, microscopy and nanoindentation, a method used to test the hardness and stiffness of materials. In research recently published in Intermetallics, the team found that the laser-deposition technique created alloys consistent with those created with traditional methods, showing that the technique is a highly efficient method that can speed up the process of identifying and refining the most promising compositions prior to creating larger quantities.
Li M, Gazquez J, Borisevich A, Mishra R, Flores K. Evaluation of microstructure and mechanical property variations in AlxCoCrFeNi high entropy alloys produced by a high-throughput laser deposition method. Intermetallics. April 2018. DOI: https://doi.org/10.1016/j.intermet.2018.01.021