Altered carbon points toward sustainable manufacturing
Feng Jiao scaled up carbon dioxide conversion process to a much larger scale
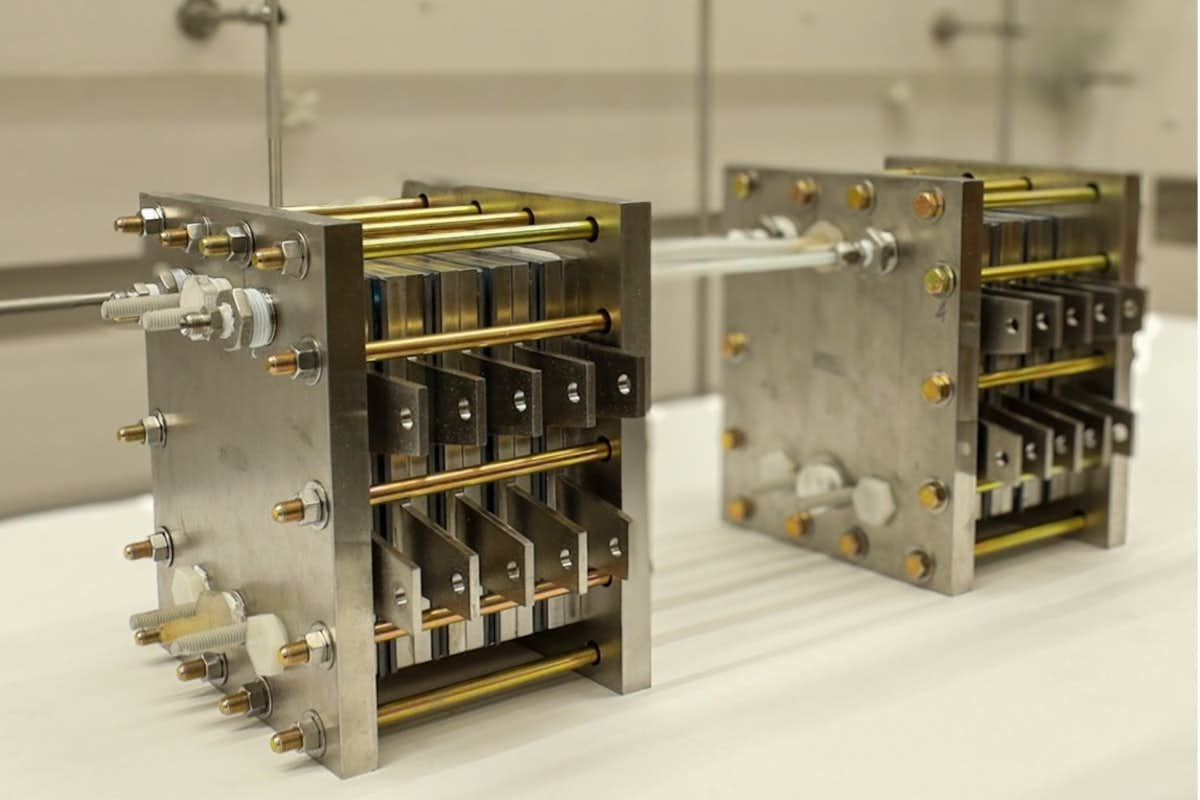
The recent spike in food prices isn’t just bad news for your grocery bill. It also impacts the sugars used in biomanufacturing, which, by the way, isn’t quite as green as scientists and climate advocates expected. Surging prices and increasing urgency for genuinely sustainable manufacturing has pushed researchers to explore alternative feedstocks.
Feng Jiao, the Elvera and William R. Stuckenberg Professor in in the McKelvey School of Engineering at Washington University in St. Louis, developed a two-step process to convert carbon dioxide (CO2) into valuable carbon-based materials used in the production of food, plastics and other commodity chemicals. Jiao’s tandem CO2 electrolysis produces acetate and ethylene. Acetate is a close relative of the more familiar acetic acid, or vinegar, which can be used as food for microbes used in biomanufacturing, and ethylene is a common component found in plastics and other polymers.
In a study published June 3 in Nature Chemical Engineering, Jiao demonstrated that his tandem CO2 electrolyzer, which was specifically engineered for enhanced production of multi-carbon products, successfully scales up to produce a kilogram of chemicals per day at high concentration and purity. This represents a 1,000% increase in scale over previous demonstrations, offering a pathway to industrial feasibility, which Jiao and his team further supported with a techno-economic analysis showing the technique’s commercial viability.
“Most work in CO2 electrocatalysis is done at a small scale, about a gram a day,” said Jiao. “Scaling up by three orders of magnitude to produce a kilogram per day, as we have done, is a big step, but still nowhere near the scale of global CO2 emission, which is gigatons per year.
“Scaling up isn’t just about system size,” Jiao continued. “We also have to address engineering challenges, for example, how to separate products and how to maintain performance when dealing with scaled up effects in temperature and transport considerations.”
Building upon insights gleaned from smaller scale experiments, Jiao’s team successfully designed and operated a CO2 electrolyzer and carbon monoxide (CO) electrolyzer in a tandem configuration. The two electrochemical reactors work in series – first converting CO2 to CO, then CO to multi-carbon products – which allows the system to be more efficient through task specialization. The electrolyzer stack performed consistently and stably for over 125 hours – a testament to its robustness, Jiao said. During this operational period, the system churned out 98 liters of acetate at high concentration and 96% purity.
A key achievement of Jiao’s system is not only enhanced production capability, but also the system's resilience against industrial impurities, a critical factor in real-world applications. This resilience ensures that the system can maintain its high performance amid challenges posed by typical industrial environments.
“This is the first step in scaling up to commercial applications,” Jiao said. “We’re trying to invent a scalable way to produce acetate from CO2, which would allow us to shift carbon feedstocks, provide economical pathways to use CO2 and turn it into something useful, and cut down CO2 emissions associated with traditional chemical manufacturing processes. This new pathway gets us very close to net-zero carbon emission.”
Back to the grocery store. If Jiao’s CO2 conversion process works at a large scale, that’s not just saving big money on buying the sugar required to feed the microbes that do the heavy lifting in biomanufacturing. It also avoids the emissions that come with agricultural production of those sugar feedstocks. Even better, producing acetate and ethylene on a massive scale could set up a circular manufacturing process where captured CO2 feeds microbes instead of contributing to harmful environmental impacts. Then, when CO2 is produced as a byproduct of biomanufacturing, it can be recaptured and reprocessed to feed the next generation of microbes.
“We’re in the process of scaling the system up again, by another order of magnitude,” Jiao said. “We’re working on fine-tuning the system, for example by using different catalysts, and improving performance by making the more stable, robust and efficient. If everything works out, we could be seeing this technology in a commercial scale demonstration in five to ten years.”
Crandall BS, Ko BH, Overa S, Cherniack L, Lee A, Minnie I, Jiao F. Tandem CO2 electrolysis: From Watt to Kilowatt-scale for enhanced acetate and ethylene production. Nature Chemical Engineering, June 3, 2024. DOI: https://www.nature.com/articles/s44286-024-00076-8.
This work was supported by the U.S. Department of Energy (DE-FE0031910).