The Plastics Problem
McKelvey engineers tackle one of the biggest environmental issues of our time
Plastic is everywhere in our lives, from furniture to food packaging to diapers. It is nearly impossible to go for one hour without touching or using something made from petroleum-derived plastic. While the material is durable and cheap to produce, its impact on the environment and on our health is so costly that researchers predict more plastic than fish in the world’s oceans by 2050, and microplastic particles are now found in human blood.
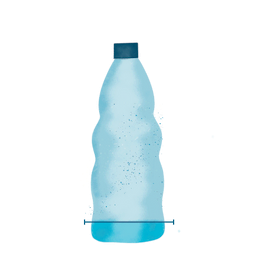
We’ve been told since at least the 1970s to “reduce, reuse, recycle,” but only about 15% of the 300 million tons of plastic waste generated annually gets recycled, while the rest ends up in landfills, where it can take hundreds of years to break down. In 2020, the U.S. Environmental Protection Agency announced its goal to increase the U.S. recycling rate to 50% by 2030 and proposed specific actions to address plastics, including reducing pollution during plastic production, improving post-use materials management, preventing trash and micro/nanoplastics from entering waterways and removing trash from the environment.
But will these efforts, coupled with existing plastic reduction and replacement efforts, be enough to make a difference?
We asked that question of some of the researchers in the McKelvey School of Engineering who are developing creative solutions to the plastics problem that they expect will lead to measurable change within our lifetime. Their answers are cautiously optimistic.
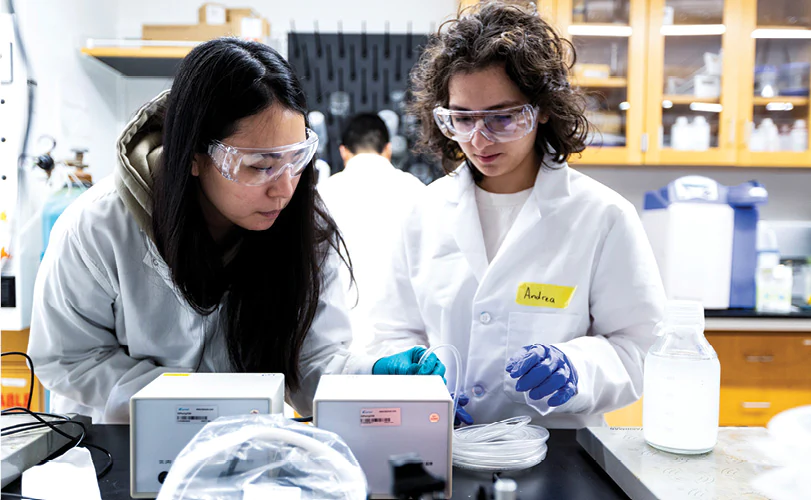
(From left) Minkyoung Jung, a doctoral student, and Andrea Carbonell, a first-year student, in Young-Shin Jun's lab.
Photo by Jerry Naunheim
Nanoplastics
In January 2024, Columbia University researchers detected and identified 240,000 plastic particles per liter of bottled water, of which about 90% were nanoplastics, or particles about one-billionth of a meter in size — a significantly higher number of particles than what scientists previously thought — raising concerns about the potential for toxicity.
Nanoplastics form when plastics break and degrade. They can generate highly reactive species particularly in light. Young-Shin Jun, professor of energy, environmental & chemical engineering, studies the effects of this degradation on the soil and water systems in her Environmental NanoChemistry Laboratory.
All of the plastic that we use will eventually enter into the environment, which will affect our health and ecosystems.
— YOUNG-SHIN JUN
“All of the plastic that we use will eventually enter into the environment, which will affect our health and ecosystems,” says Jun, who also is the chair of the Science and Technology Subcommittee of the American Chemical Society’s Committee on Science.
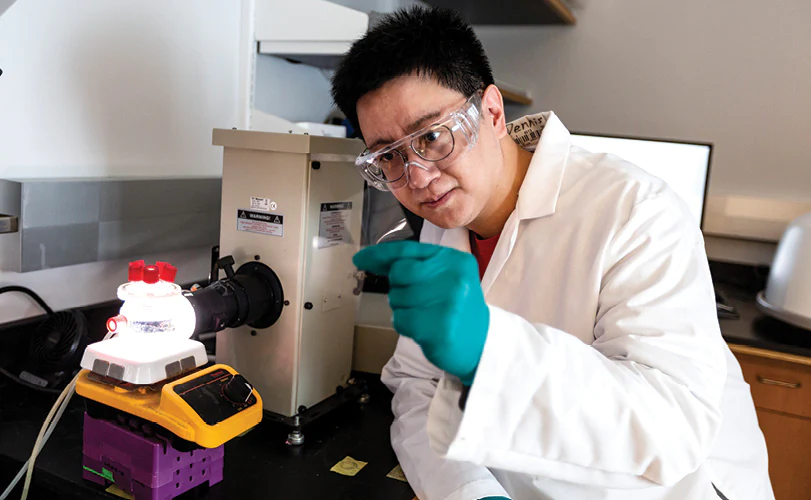
Ping-I-Chou, a doctoral student, works in Young-Shin Jun's Environmental NanoChemistry Lab, where they study nanoplastics in the environment. Photo by Jerry Naunheim
Recently, Jun and her team analyzed how sunlight breaks down polystyrene, a nonbiodegradable plastic from which packing peanuts and disposable utensils are made. The research showed that when exposed to light, nanoplastics generate reactive oxygen species, rapidly facilitating a transformation from aqueous manganese ions into manganese oxide solids. This unexpected reaction can occur even faster with smaller nanoplastics, changing the fate and transport of nanoplastics themselves and other co-existing contaminants, such as organic contaminants and heavy metal ions, and affecting the environmental quality.
Using creative materials
One way to address the plastics problem is to create biodegradable plastic from materials other than petroleum — whether it be renewable materials, recycled materials or new materials created from natural resources.
“We are a long way from being able to solve the problem, but it’s really urgent that we start doing transformative work now,” said Guy Genin, the Harold and Kathleen Faught Professor of Mechanical Engineering and a faculty member in the school’s Synthetic Biology Manufacturing of Advanced Materials Research Center (SMARC). “Relying on oil as the major feedstock for the production of fuels, chemicals and materials is problematic — we will eventually need new resources. But it’s hard to match the price and properties of existing plastics derived from oil.”
SMARC is co-directed by Marcus Foston, associate professor, and Fuzhong Zhang, professor, both in the Department of Energy, Environmental & Chemical Engineering. Partially funded by a five-year, $3.6 million grant from the National Science Foundation, the center’s collaborators plan to develop a new class of biologically synthesized, protein-based and biodegradable materials that harness themes from nature to replace traditional petroleum-derived plastics. Roman Garnett, associate professor of computer science & engineering, is also on the team, along with researchers from Northwestern University, Iowa State University and University of South Florida.
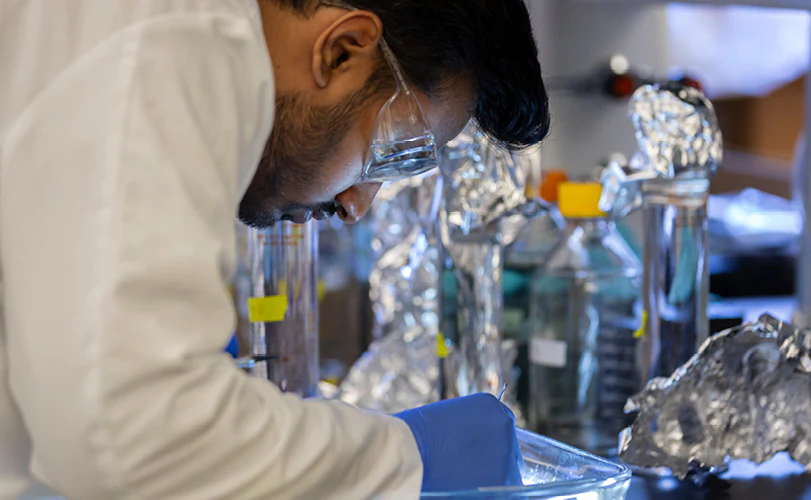
Zhang, an expert in synthetic biology who has used bacteria to create renewable fuels and other materials, is now using bacteria to create renewable plastics that will not harm the environment.
“We are aiming to create advanced materials that degrade naturally or can be recycled more efficiently and in an environmentally friendly and cost-effective manner,” he said. “Biological engineering provides a solution to address that.”
Zhang’s lab is working to achieve new materials made from renewable feedstock independent of petroleum through a biological manufacturing process and has tunable properties to meet the needs for different applications. One product his lab is making is adhesives for medical products, such as surgical glues, from biological materials. His team has mimicked the sticky proteins secreted by mussel feet that allow them to stick to different surfaces under water, making them into hydrogels that are biocompatible and durable.
Joshua Yuan, the Lucy & Stanley Lopata Professor and chair of energy, environmental & chemical engineering, and collaborators at Texas A&M University are using carbon dioxide, a waste product from greenhouse gas emissions, to produce biodegradable plastics. This system, which took more than two years to create, uses carbon dioxide to produce intermediates that can feed bacteria to grow and produce bioplastics. His team also uses diverse waste streams like food waste and black liquor to produce bioplastics. If able to be scaled up to an industrial scale, the process could help to replace petroleum-based plastics with products that have fewer negative environmental impacts.
Yuan and his team also are working to make biopolymers, including lignin and cellulose, to improve biodegradability and the mechanical performance of biodegradable plastics. He recalled a trip to Hawaii, where nondegradable plastics are banned from use.
“The plastic bags there were made of degradable materials, but they were not as good as regular plastic bags and were difficult to handle,” he said. “The faculty in our department are working hard to make these degradable materials perform as well as petroleum-based plastic.”
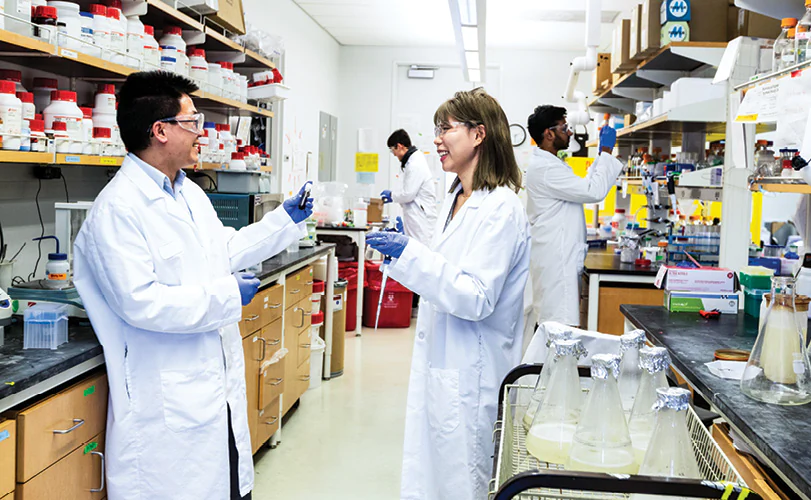
Upcycling
Since plastic can be recycled only a few times, researchers are looking for ways to upcycle, or reuse a product or material for a new purpose. McKelvey Engineering researchers are looking for a way to break down plastics to make a new materials, therefore creating a circular economy. For example, polyethylene, the most produced plastic, can be broken down to be used as valuable lubricants, Foston said. However, due to economics and lack of industry buy-in, no large-scale operation exists to upcycle plastic, and thus researchers must address barriers to adoption.
“Our center is designed to bring in industry to influence early-stage science,” Foston said. “These problems require transdisciplinary research that depends heavily on the way in which business and markets work, on how people adopt technologies and barriers to those technologies.”
We have potential solutions, but how much do they cost?
While many of these alternative plastics may be better for the environment, they come at a cost.
“If the cost is not competitive to current petroleum-derived plastics, you will not see renewable plastics in the market,” Zhang said. “And that cost comes from multiple aspects: the feedstock, the process, overall yield, scalability, capital costs, operating costs and many others.
“Very often, products with large market sizes have low profit margins, whereas those yielding higher margins trend to cater to limited market segments prone to rapid saturation,” he continued.
“The transition from petroleum-based plastics to renewable, degradable materials is likely going to be a progressive evolution, initially emerging through expensive specialty materials, with gradual advancements toward materials suitable for widespread applications,” he said.
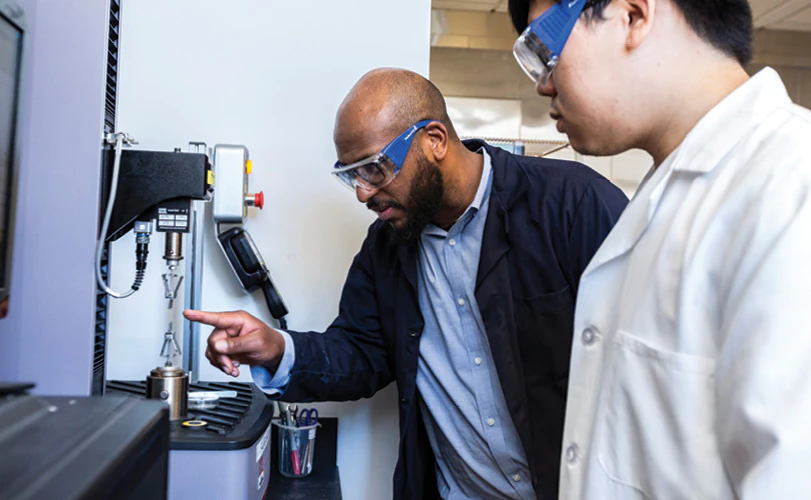
Can plastic alternatives make a difference?
“I don’t think the answer is a simple yes or no,” Zhang said. “As an engineer, after we learn from all the previous successes and failures, it’s going to be a long path, and if we’re trying to quantify things, how do we define success?”
Many companies have launched everyday household products, such as laundry and dishwasher detergent sheets and personal care products, that claim to be “plastic free.” However, some contain PVA, or polyvinyl alcohol, a dissolvable synthetic polymer, or plastic. And paper bags aren’t always a better choice than plastic bags, since getting paper bags to far-flung locations can take more oil than is used to produce plastic bags.
While composting and recycling have benefit, these changes require people to adopt them, Foston said. But for other products, we must look at the long view, he said.
“When you do a lifecycle analysis of a paper straw, there is more CO2 released in producing a paper straw than a plastic straw, but we’re not putting plastic back into the environment,” he said. “If we had the right kind of disposal system that kept the plastic straw from getting into the environment, then it would be a better option.”
Paper straws have also been found to contain poly- and perfluoroalkyl substances (PFAS), also known as “forever chemicals” because they break down very slowly and can remain for millennia in the environment, as well as having potential harmful effects on human health, according to a 2023 study in Food Additives and Contaminants.
If we had the right kind of disposal system that kept the plastic straw from getting into the environment, then it would be a better option.
— MARCUS FOSTON
The public’s part
In 2008, Frito-Lay introduced a compostable bag for Sun Chips made from a biodegradable corn-based material that took four years to develop. However, consumers quickly deemed it too loud, with one user measuring its crinkly noise at 95 decibels, which is in the harmful range. In 2021, the company launched a new compostable bag in its quest to make all its packaging recyclable, compostable, biodegradable or reusable by 2025. But will consumers accept it this time?
Foston said it’s all about understanding human behavior and the systems humans have built, which is why SMARC has social scientists and communications professionals on its team.
“Our job as engineers is to figure out how to address the existential threat that’s two, three or four generations away,” Foston said. “In free market economies, such as those in the U.S., how do we design solutions that fit into our fundamental understanding of those market dynamics? How do we make materials that are as cheap as or cheaper than petroleum-derived plastics while having industries and consumers value those same materials beyond cost? Can we educate our population so that they understand these new materials and how they address existential threats, maybe so much so that they are willing to pay more?”
What’s next?
McKelvey Engineering researchers, within SMARC or in their own labs, will continue to look for solutions to mitigate this global problem.
“Our job is to figure out how to explore the massive design space that nature has been accessing through evolution by trial and error, but we can’t wait for evolutionary time scales to do it,” Genin said. “SMARC is injecting physics-based machine learning and modeling into this process to produce novel and sustainable materials with properties such as durability, strength, toughness and thermal conductivity that outperform polymers made with petroleum or even found in nature.”
Not only is the plastics problem a focus of research in McKelvey Engineering, but it is also at the core of the university’s Here and Next strategic plan, launched in 2022.
“WashU has an excellent foundation in this area and has our story to tell, and with continuous advancement and support from the central administration and from the McKelvey School of Engineering, we have rallied the support to become a national leader in this area,” Yuan said.
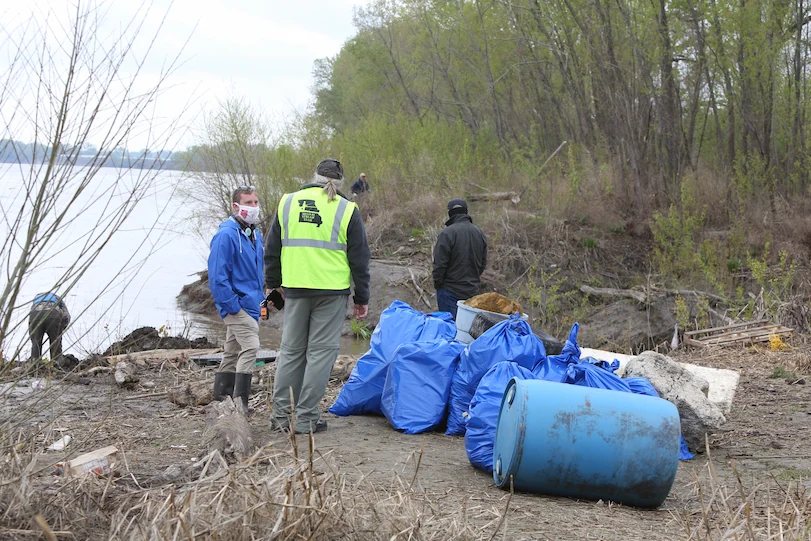
Mississippi River plastics
In September 2018, mayors from cities along the Mississippi River committed to reduce plastic in the Mississippi River Valley 20% by 2020. The Mississippi River flows more than 2,000 miles from headwaters in Minnesota to the Gulf of Mexico and generates more than $400 billion in revenue and provides drinking water to more than 20 million people and 50 cities. Volunteers collected and tracked waste from the river for several months and logged nearly 175,000 items. Of those, 75% were plastic; 9% were paper; 7% metal; 5% glass; 2% PPE – masks, wipes, gloves. The top 10 items were cigarette butts, food wrappers, beverage bottles, foam fragments, hard plastic fragments, paper and cardboard; plastic bags, aluminum or tin cans; foam or plastic cups, and film fragments.