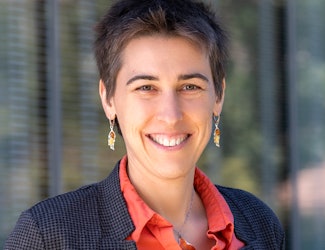
Patricia Weisensee
Mechanical Engineering & Materials Science
- Phone
314-935-7951 - Office
Jubel Hall, Room 203M - Lab location
Jubel Hall, Room 233
Education
PhD, University of Illinois at Urbana-Champaign, 2016Dipl.-Ing., Technical University Munich, 2013
MS, University of Illinois at Urbana-Champaign, 2011
Expertise
Studies heat transfer and fluid dynamics in multiphase systems for energy and manufacturing applications
Focus
Experimental thermo-fluid dynamics using high speed imaging, including phase change heat transfer, droplet impact, wetting, and capillary transport in porous media.
Research
Weisensee’s work focuses on understanding the interplay of fluid dynamics, heat transfer and liquid-solid interactions of droplets and other multi-phase systems. Practical applications of interest are phase change heat transfer for thermal management, thermal storage, and water harvesting, metallic additive manufacturing, and droplet interactions with biological and natural systems.
Biography
Professor Weisensee joined Washington University in St. Louis as an assistant professor in January 2017. She earned a doctorate in mechanical engineering from University of Illinois at Urbana-Champaign (UIUC) in December 2016. Weisensee earned a Diplom-Ingenieur (B.S. + M.S.) in mechanical engineering with high distinction from TU Munich, Germany, in 2013, where she was awarded the Siemens Energy Award for her work on condensing steam bubbles in subcooled flowing water. During her Diplom studies, she was a fellow of the German National Academic Foundation (Studienstiftung des Deutschen Volkes). Weisensee also holds a master’s in materials sciences from UIUC (2011).
Video spotlight
Affiliations
Undergraduate research opportunities
Contact Patty Weisensee for more details about the following projects:
1. Studying the effects of electrostatic charging for water droplets coalescing in oil
During condensation experiments on so-called lubricant-infused surfaces (a micro- or nanoporous surface that is covered by a thin (few µm) layer of oil), we noticed two very peculiar things: 1) the water droplets coalesced, i.e., merged, very easily when they were condensing on a Krytox oil, but didn’t coalesce and formed a droplet raft on silicone oil, and 2) we were able to move droplets across the surface without touching them (i.e., by bringing a finger close to the droplet, but not making physical contact) on silicone oil, but not Krytox oil. This leads us to believe that spontaneous charge separation occurs when the water and oil come in contact with each other, which can then cause electrostatic forces to act on the droplets. While this is a known phenomenon in itself, it does not explain the observed coalescence/non-coalescence behavior. As part of this research project, the student will continue quantifying the amount of charging that occurs and run experiments with bulk oil baths, into which water droplets are injected, in order to better understand charging and coalescence behaviors. No specific knowledge or lab experience are required.
2. Preparation of micrometer-sized dyed polymer spheres to study thermal-fluidic processes in additive manufacturing
Additive manufacturing (AM) of metals presents enormous opportunities for the production of geometrically complex structures, particularly for highly specialized, low production volume components where the costs of investing in dedicated tooling are prohibitive. While 3D printers for polymers are commercially available even for private households, AM of metals still suffers from inconsistency in part quality, including surface finish and porosity. Mechanical properties, microstructural characteristics, and feature resolution are strongly material and process dependent. However, the limited understanding and characterization of the underlying physical processes during deposition inhibit further development of metallic AM. Specifically, the interplay of powder impact dynamics and subsequent thermal interactions on the melt pool remains largely elusive; in part because of the opacity of metals. Our lab thus aims at developing and testing a transparent model system that uses polymer powder particles, which can be visualized using high-speed imaging, and their impact, melting, and mixing dynamics studied. As part of this research opportunity, the student will refine preliminary procedures to produce and spray such polymer powder particles. Time-permitting, the student can also conduct preliminary visualization experiments to study impact and melting behaviors of these particles. No specific knowledge or lab experience is required.
3. Studying the effect of substrate stiffness (or rather: softness) on metal droplet impact dynamics
Additive manufacturing, or 3D printing, of metals and polymers is increasingly displacing traditional manufacturing techniques. However, printing of multi-material parts, for example of hard/soft hybrid components used in biomedical and (soft) robotics applications, remains a challenge, primarily due to the poor adhesion between the two materials. Material jetting, a process similar to inkjet printing, is the most promising candidate to fabricate integrated metallic and polymeric components, whereby the quality of the final part is dictated by the spreading, solidification, and adhesion/fusion behavior of the individual droplets. In this work, we focus on quantifying the interactions between impacting metal droplets and a soft elastomeric substrate (i.e., PDMS). As part of this research experience, the student will continue experiments previously conducted by another undergraduate student, which involves a) the fabrication of PDMS samples of varying stiffness, b) quantifying the deformation of the sample when a droplet is sitting on top of it using fluorescent confocal microscopy, and c) studying the impact dynamics of metal droplets (such as spreading and retraction) using high-speed imaging. No specific knowledge or lab experience are required.
4. Evaluating the suitability of refrigerant mixtures for efficient condensation
Every year, trillions of kWhs of energy are lost as waste heat. In times of severe climate change, becoming carbon-neutral within the next few decades will necessitate the more efficient use of resources, including power generation from low-grade heat sources or more efficient air conditioning and refrigeration (A/C-R) systems. In all of these applications the low rates of heat transfer during condensation of the working fluids (mainly refrigerants) limit the overall system efficiency and increase size and cost of the condenser units. The poor thermal performance stems from the low surface tension of these non-aqueous working fluids, which causes them to condense as a film, creating a thermal resistance between the vapor and the condenser coils. One possible solution to overcome this challenge lies in the use of dilute refrigerant mixtures, which – due to a unique temperature-dependence of mixture properties – might be able to increase heat transfer rates dramatically by inducing instabilities that lead to the formation of individual droplets. As part of this research experience, the student will participate in the lab’s activities that are evaluating and quantifying the suitability of certain mixtures to promote the so-called “Marangoni condensation”. Experiments might involve measuring the surface tension of different mixtures as a function of concentration and temperature, assisting in validating the condensation setup using water and steam, or conducting and analyzing condensation experiments with said refrigerant mixtures. No specific knowledge or lab experience is required.